Collection Level
Most large libraries spend considerable sums of money on the commercial binding of periodicals, the first-time binding of paperbacks, and the contract rebinding of circulating books to preserve their collections for posterity. Careful analysis of the effect of conservation decisions on the longevity of collections can minimize future problems and save money.
Binding periodicals
Periodical binding is usually conducted under contract via vendors for most libraries. In many cases, decisions are made on the basis of short-term practicability, volume dimensions, and an impression of patterns of use. However, binding is done after the current use on the unbound issues has been expended, thus some of the massive and inflexible structures designed by binders for heavy use are commissioned mistakenly on the basis of patterns of use before the unbound issues can be protected by such heavy-duty bindings. Inflexible leaf attachment methods, such as oversewing, stab-stitching, and drill-and-sew, actually hasten the destruction of the bindings as they render photocopying, microfilming, and digital scanning almost impossible without the cutting of sewing to allow the leaves to open well enough to see the text at the inner margins.
Most periodicals produced today are not in signature form and cannot be sewn through the section folds. The only practical way to avoid inflexible, through-the-surface sewing methods is through the use of double-fan adhesive binding, in which single leaves are fanned mechanically in both directions, and an adhesive line of 0.5 millimeters is applied between each leaf. Owing to the cost of the machinery required, commercial binders in developing countries often fan leaves by hand.
The appropriate binding for adhesive structures is a flat-backed, flush construction, with binders’ boards glued directly onto the outside of the endpapers about 1 centimeter from the back edge. The backbone is lined with kraft or wrapping paper, and a piece of pre-lettered book cloth is glued directly on top of the backbone extending approximately 6 centimeters onto the boards. The bound volume is lightly trimmed to level the edges.
This form of binding is inexpensive and dimensionally stable (it cannot sag on the shelf). Periodicals may be bound in the library with minimal equipment and easily opened.
Binding paperbacks
A large percentage of new books entering libraries are now in paperback form, which poses a dilemma to the librarian. Because paperbacks are invariably monographs and generally new, it is impossible to base binding decisions on patterns of use. Expending binding funds on a book that may never be used is wasteful, but not binding paperbacks that may be heavily used risks damage and possible loss. A partial answer to this problem is stiffening and pamphlet casing.
Stiffening
The tools needed for stiffening are a bone folder, scissors, a paper shear (small guillotine), a glue brush, a needle, and linen thread. If a large number of paperbacks must be processed on a regular basis, some thought might be given to investing in a power paper cutter and a gluing machine. The materials for stiffening consist of PVA adhesive, white-lined board approximately 2 millimeters thick, sized cotton hinge cloth cut 1.5 centimeters in width and the height of standard board sizes, and sheets of waxed paper or sheets of plastic. The boards should be bulk cut to six standard sizes: 19.5 x 13 centimeters, 21 x 14 centimeters, 23 x 15 centimeters, 25.5 x 17 centimeters, 28 x 21 centimeters, and 33 x 25 centimeters.
Stiffening begins by sizing paperbacks according to standard board sizes. The covers of the paperbacks are opened and the inner joint creases set with a stroke of the bone folder. Two pieces of hinge cloth are glued and laid down, with the inner joints extending onto the text block by approximately 0.5 centimeters and onto the inside of the cover 1 centimeter.
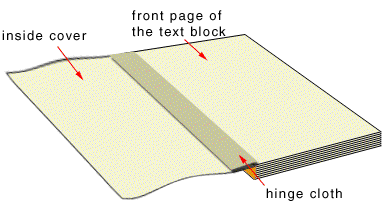
Two boards of the appropriate size are glued on the unlined surface, and one is laid with the glued side uppermost onto the text block about 0.5 centimeters from the inner joint.
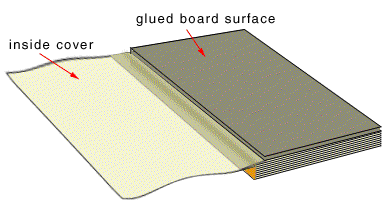
The cover is carefully laid down onto the glued surface and rubbed down with the folder, lightly setting down the outer joint with the folder edge.
A piece of wax paper is laid over the outside of the cover, and the paperback turned over to repeat the process on the other side.
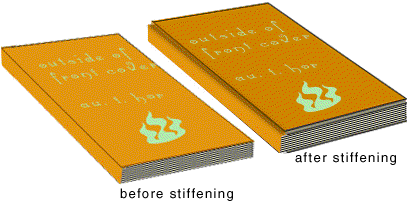
The processed paperbacks are stacked on top of each other and separated by sheets of wax paper to prevent sticking. When the stack is dry, paperback edges may be lightly trimmed on the power paper cutter to make the covers flush, or the protruding edges of boards can be cut off with a hand shear (guillotine).
Pamphlet cases
Pamphlet cases may be constructed or purchased from a vendor for single-section items such as folded brochures. This method requires white-lined boards cut to standard sizes, paper spine strips of any stout paper cut to the height of the boards and 2 centimeters wide, acid-free paper to line the inside of the opened-out case with a margin of 0.5 centimeters, and strips of book cloth 5 centimeters in width and the height of the boards plus a turn-in of 3 centimeters.
The book cloth is glued and the paper spine strip laid onto its center.
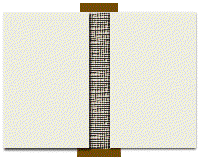
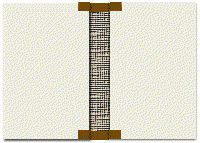
The boards are placed onto the glued cloth against the paper spine strip and turned-in at the head and tail.
The glued surfaces are rubbed down with the folder. The lining paper is glued, positioned inside the case, and carefully set down on the spine paper. After the pamphlet case dries and is folded in half, the pamphlet is sewn into the case with a three- or five-hole stitch.
Pamphlet cases can be made in large numbers. The gluing machine can be usefully employed if the work is organized to take advantage of multiple stock cutting and productive hand processing.
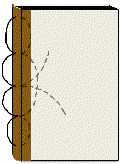
Mass de-acidification
All libraries and archives must cope with the problem of brittle paper or highly acidic paper in the process of turning brittle. Beyond reformatting, little can be done for entire collections that suffer from brittle paper, but there are remedies for acidic paper that is not yet brittle. For many years, a great deal of effort has gone into the development of processes that can neutralize the acids in paper that still has some measure of flexibility. Manual methods of alkalizationrequire that books be unbound into leaves, and as this is impractical for entire collections, mass de-acidificationsystems have been developed. Mass de-acidification should chemically stabilize paper without damaging the rest of the book. Other requirements of this process are the ability to process large numbers of books in a short time, low unit cost, safety, and environmental friendliness.
Solvent immersion systems
A number of processes for achieving these ends were developed with varying degrees of success. In the late 1950s and early 1960s some success with ammonia gas was reported by scientists in the Soviet Union, but information was sparse and the process soon abandoned. Between 1970 and 1977, a process was developed by the Barrow Research Laboratory that utilized morpholine (an organic liquid commonly used as a solvent in cleaning solutions) in combination with water vapour. Although morpholine seemed at first to satisfy some of the criteria, books so treated returned to an acid state in the presence of high humidity.
A process that has been operating successfully since 1981 is Richard Smith’s magnesium methoxide system, installed in the records conservation department of the Canadian National Archives. The process involves drying books in a vacuum dryer, de-acidifying them in a solvent solution by immersion, and vacuum drying to remove the unused solvent. A drawback to this system is that books must be sorted to avoid processing those with soluble inks, dyes, andbookcloths.
In 1976, Kelly and Williams of the US Library of Congress designed a vapour-phase process employing diethyl zinc (DEZ). An organometallic compound, DEZ successfully de-acidifies paper leaving an alkaline reserve of zinc oxide. Because of the extremely high volatility of the chemical, tests were abandoned by the Library of Congress and subsequent commercial production efforts by Akzo, a Dutch chemical company were not successful.
The two most effective systems today are the Bookkeeper process, operated by Preservation Technologies of Pennsylvania, USA, and the Battel system, now operated by Zentrum für Bucherhaltung (ZFB) of Leipzig, Germany. Both utilize solvent immersion, and results from accelerated-aging tests seem to confirm their usefulness. In 1994, a rigorous evaluation of the Bookkeeper process led the U.S. Library of Congress to award a de-acidification contract to Preservation Technologies. In this process, books immersed in an inert liquid carrier absorb magnesium oxide particles.
But these mass de-acidification systems have their drawbacks. Not only are they costly, but construction and installation requirements are difficult for libraries to manage. What would help is a system that can easily be installed on site, and with a low unit cost that eliminates the need for pre-selection for treatment.
Paper strengthening
De-acidification neutralizes acidic paper but does not strengthen deteriorated paper. Other than paper splitting and lamination, there has been no major advance in paper strengthening. In the early 1980s, the American Nova Tran Corporation conducted experiments with parylene, a coating developed for electronic equipment, but the high cost of the process renders it impractical for mass use. In the late 1980s, the British Library began paper strengthening experiments with a graft polymerization process that seemed promising but does not seem to have developed beyond the experimental stage.
The ZFB company of Leipzig has successfully mechanized a manual paper-splitting process used by bookbinders for more than 150 years (http://www.zfb.com). This process splits a sheet of deteriorated paper in two between glued rollers. A strengthening layer is inserted between the two halves, which are then fused. This process does not noticeably affect the appearance of the paper.